Federal Center South Building 1202
SENV 7006

Building Integrity

Qualitative
Quantitative

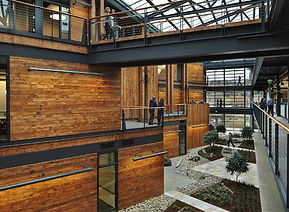

Structure


Materials of Construction
Material reuse, long-term maintenance, and life-cycle cost were three important material seletion criteria. The site's corrosive location along a salty waterway and adjacent to a cement plant, was an important additional consideration for the exterior cladding system.
Ferritic Type 444 stainless steel containing 2% molybdenum was selected for the facade. Due to its molybdenum content, Type 444 has better corrosion resistance in the demanding environment than the lower cost Type 304 stainless steel. Its corrosion resistance is similar to that of the better known, but more costly, Type 316 which also contains 2%molybdenum. An additional factor in selecting Type 444 was its ability to be readily colored electrochemically to the pewter color required by the architect. Also, Type 444 can be brake formed into a variety of oarts for siding and cladding, but requires a more enerous bend radius than Type 316.
Integrated Design
The oxbow design solution provides the greatest flexibility for work groups to expand and contract as needed, while the narrow floor plate optimizes daylight penetration.
The exposed “diagrid” structure and mechanical systems of the 1202 building exemplify the engineering rigor, strength and stability of the USACE’s mission of Building Strong.
In response to the ARRA funding requirement to reuse portions of the existing warehouse that previously stood on the site in the design of the new 1202 building, approximately 100,000 board feet of salvageable structural timber and 200,000 board feet of decking (92%) was reclaimed to form the commons foundation, structural system, and interior cladding.
As a part of the project’s effort to reuse existing materials, the design-build team reclaimed significant amounts of timber from a demolished warehouse on-site. To optimize the use of the available materials, the engineer suggested the use of a composite design for the floor system. Since this was the first time this type of design was used in the United States, the team built a mock-up in the adjacent warehouse to test the structural integrity of the proposed composite timber-concrete system.
Construction waste is one of the best-known culprits contributing to the domestic solid-waste stream; building activity contributes about 40% of the total solid-waste stream. This project is not a typical example of the industry, achieving a 99% construction-waste diversion rate.
Material
Procedure
-
For rating system documentation purposes, maintain a list of reused and salvaged materials and corresponding costs.
-
The percentage of salvaged and reused wood employed on a project is based on the cost of salvaged/reused materials divided by the total cost of materials. The cost will be the actual cost paid or, if the material came from on-site, the replacement value. The replacement value can be determined by pricing a comparable material in the local market (excluding labor and shipping). When the actual cost paid for the reused or salvage material (from either on-site or off-site) is below the cost of a comparable new item, use the higher value in the calculations.
-
Furniture may be included if it is used consistently in the calculations of both salvaged materials and total materials used on a project. Percentage salvaged/reused materials =cost of reused materials ($) total material cost ($) × 100
Through collaborative efforts, the team created and tested three new sustainable products utilized in the building and ready for the market.
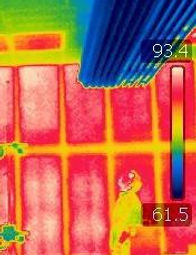
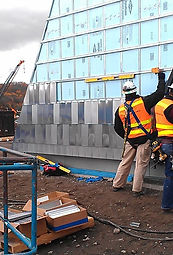
Given the engineering focus of the occupant’s material design and selection, the design focused on exposing structural and HVAC systems, while using durable and sustainable materials. The office portion highlights structural steel, a highly recyclable resource, while the atrium features reclaimed wood.
Compact form with reduced envelope area and a three story approach reduce the footprint and materials of the project. The diagrid structure reduces steel use, and allows for “progressive collapse,” reducing damage in catastrophic events.
Approximately 200,000 board feet of structural timber and 100,000 board feet of decking was reclaimed from the decommissioned on-site warehouse. Using a phased demolition process, wood components were individually harvested from the warehouse. The team pulled nails, unfastened bolts, removed brackets and devices, trimmed out fractures, and sorted the wood before it was shipped to a local mill for structural grading and fabrication.
Composite beam construction of the commons optimized the use of the available salvaged lumber with lag bolts from the wood structurally engaging a reinforced concrete topping slab. This was the first time this design was used in the U.S. and the team built a mockup in the adjacent warehouse to test structural integrity of the proposed composite timber/concrete system.
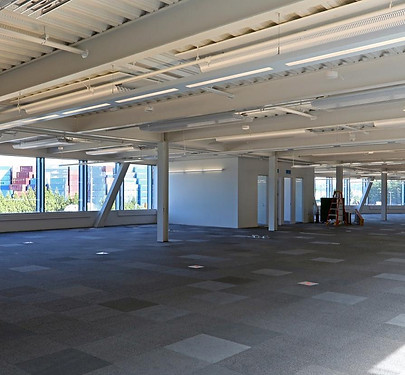
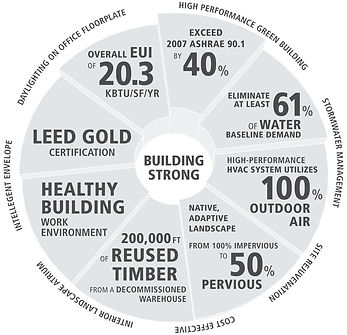

Reuse Existing Piles
Structure
© 2016 by CUHK SENV 7006. Group 1 created with Wix.com